ISO 9001 is an international standard for Quality Management Systems (QMS). It helps businesses simplify their processes, work more effectively, and keep improving. The focus is on meeting customers’ needs and providing high-quality products and services to boost customer satisfaction.
Achieving certification can improve your business reputation, build customer trust, and open up new market opportunities.
ISO 9001 is a valuable tool for any business or organization that wants to enhance the quality of its offerings and remain competitive.
Keep reading to learn how to avoid common mistakes when setting up a QMS with ISO 9001:2015. We’ll give you tips to help you avoid these issues.
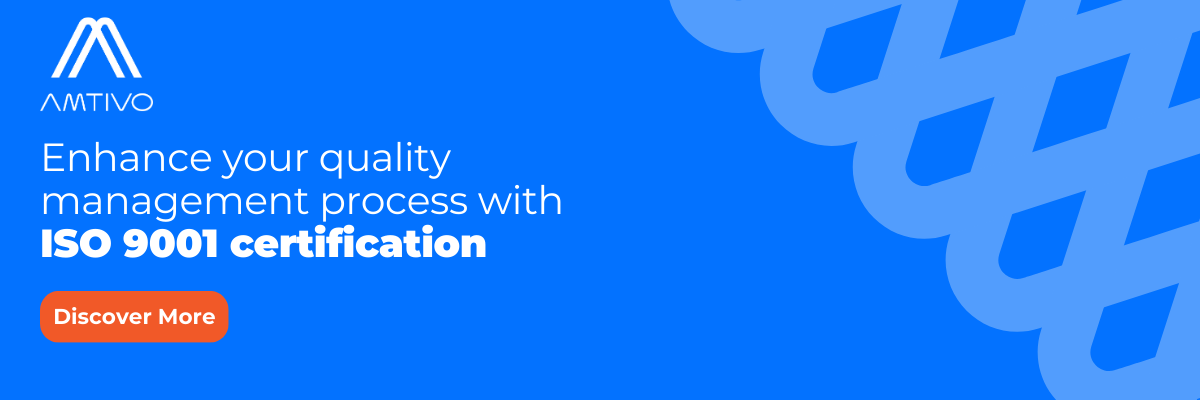
1. Lack of Senior Management Commitment
Having top management involved is key when setting up a Quality Management System (QMS) aligned to ISO 9001. Their involvement helps align the system with the company’s core goals and establishes a culture focused on quality. Without their active participation, the QMS may struggle with unclear objectives and direction. Leaders also need to provide the needed resources and encourage all employees to take part in ongoing improvements, helping them feel engaged and positive about the company’s quality efforts.
Try these tips:
- Get top management involved from the start of the process so they are enthusiastic about the process.
- Discuss how ISO 9001 can support business aims, emphasising advantages like cutting costs and boosting customer satisfaction.
- Define the leadership team’s roles and duties within the QMS, giving them time to fully understand them.
- Provide examples and results from other businesses that have benefitted from ISO 9001 to show how it could improve your own organization.
2. A Lack of Internal ISO Knowledge
A lack of knowledge can slow down your ISO 9001:2015 certification process, so it’s important to train everyone involved.
Understanding the standard’s rules and ideas is crucial for creating a quality-focused culture and can help lower resistance to change. Well-trained employees can follow procedures better, leading to fewer mistakes.
Try these ideas to improve internal knowledge in your organization:
- Hold regular training sessions to keep everyone informed about updates or changes.
- Choose training methods that fit your particular team and their preferences. Consider workshops, online courses, or in-person sessions.
- Gather feedback from employees to continually refine and enhance the training process.
- Promote a culture of ongoing learning by offering mentoring programmes or refresher courses.
Find out about our ISO 9001 training courses.
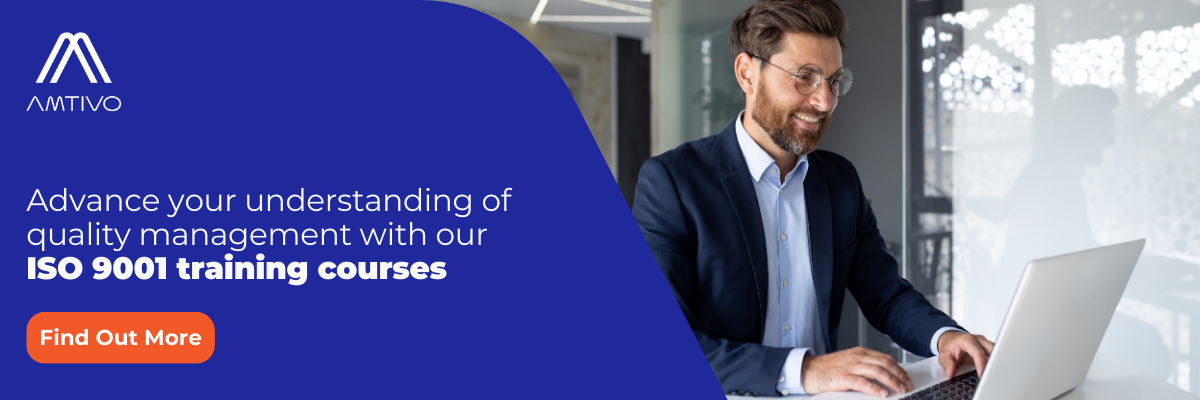
3. Keeping Inadequate Records
Even though it can be time-consuming, keeping detailed, accurate, and up-to-date records is crucial for ISO 9001 certification. Well-maintained documents show your commitment to a strong Quality Management System (QMS).
Without organized and current records, it’s hard to prove that your processes are consistent and help you to discover areas for improvement. It also makes it tougher to fix any issues that are identified.
These tips could make for a smoother ISO 9001 certification process:
- Create clear instructions and establish the use of templates to produce uniform documentation, making it easier for both staff and auditors to understand processes.
- Conduct regular reviews to check that documents accurately represent present practices and meet the ISO 9001:2015 standard’s requirements.
- Set up a system for updates and versions. Make sure all employees know how to manage their documents so they don’t end up with multiple or outdated versions.
- Securely store documents, while ensuring they are easily accessible to those with authorised access.
4. Neglecting a Joined-Up Approach
Understanding and managing processes as interconnected systems is essential for achieving ISO 9001 certification. This approach allows different teams within the organization to work effectively together to meet shared goals.
Without it, maintaining consistent quality and spotting areas for improvement can be more difficult. Try these ideas for a more cohesive approach:
- Evaluate processes regularly and gather customer feedback to ensure alignment with the organization’s goals and needs.
- To avoid confusion, clearly define each team member’s role and how each process works within your organization.
- Organize regular meetings and workshops to improve understanding and encourage teamwork across different departments, ensuring everyone is on the same page and working efficiently together.
- Use visual tools like charts or maps to track workflow and identify areas where a process is affected.
5. A Reluctance to Adapt Internal Processes
Opposition to change is common in any business, but it can significantly hinder the implementation of ISO 9001:2015—and prevent your organization from fully experiencing its benefits.
This resistance can result in missed opportunities for improvement and innovation, which can negatively impact both employees and certification efforts.
To avoid this, try the following:
- Keep communication channels open so that staff can share concerns and brainstorm solutions, fostering transparency and early problem-solving.
- Build a culture that values input and collaboration, strengthening teamwork and allowing you to address challenges effectively.
- Encourage leaders to be actively involved in the certification process to set a strong example, reinforcing its importance and motivating employee engagement.
- Share success stories that highlight the benefits of ISO 9001, encouraging a positive view of the changes needed for certification.
6. Not Enough Internal Audits
Internal audits are vital for preserving the integrity of your QMS. They help uncover issues and evaluate the effectiveness of your processes. Internal audits also prepare the business for important external audits.
Skipping internal audits can lead to unnoticed non-conformities, while opportunities for improvement can also be missed.
Consider these ideas to help ensure your internal audits are well-planned and efficient:
- Plan audits thoroughly by clearly defining their scope, objectives, and criteria.
- Select suitable auditors, whether internal or external, to conduct the audits based on their expertise and impartiality.
- Carefully review audit results and share the insights with relevant teams to help improve decision-making.
- Ensure actions taken to correct issues are followed up on to verify their success and promote continual improvement.
7. Overlooking Continual Improvement
Focusing on continual improvement is fundamental to ISO 9001 requirements. Without this crucial focus, productivity and quality can stagnate, and your business could fail to meet customer expectations.
Ignoring inefficiencies can also lead to rising operational costs. Consider these ideas to bring your organization’s focus back to continual improvement:
- Develop and track key performance indicators (KPIs) to evaluate performance and pinpoint areas for enhancement.
- Encourage staff to actively contribute ideas for improving and innovating processes.
- Train employees on the Plan, Do, Check, Act cycle to give them the tools to drive improvements.
- Conduct regular audits and management reviews to evaluate process effectiveness and find opportunities for improvement.
Proactive measures and continual learning are vital for successful ISO 9001 implementation.
Amtivo can help with a successful implementation—read our ultimate guide to ISO 9001 to discover more.
We have created an essential checklist that offers a comprehensive insight into what is needed to achieve certification in the ISO 9001:2015 standard.
Download our free ISO 9001 checklist to get started.