A Quality Management System (QMS) can improve the efficiency and dependability of any business, whether it’s a new small business or a large, established company.
In this guide, we’ll explain what a QMS is in simple terms, why it’s worth your time to implement one, and how to get it up and running.
We’ll also discuss some other quality-related standards you might have heard about, like ISO 9001, ISO 13485, IATF 16949 and AS9100, and what they mean for your business.
What Is a QMS?
A Quality Management System (QMS) is a formal system that sets out how an organization should work to consistently make products or provide services that meet customer needs and regulatory requirements. It documents the processes, procedures, and who is responsible for meeting quality goals.
At its heart, a QMS creates a quality culture in an organization. It helps to ensure every employee knows their job in maintaining high standards to achieve company goals.
With a good QMS in place, businesses can better manage risks, streamline operations, and improve customer satisfaction.
Common Quality Standards, Methodologies and Approaches
- ISO 9001: A globally recognised standard for Quality Management Systems, applicable to organizations of any size or sector. It is suitable for any business, big or small, in any industry.
- Six Sigma: A methodology used to reduce process variation and defects. While not a formal QMS standard, it can complement QMS initiatives.
- Total Quality Management (TQM): An organization-wide approach that aims for continual improvement in all areas of operations.
Some industries have their own specific ISO standards:
- ISO 13485: This standard applies to quality management systems for medical devices, helping businesses to deliver products that meet customer and regulatory requirements.
- IATF 16949: Focused on the automotive sector, this technical specification aligns with ISO 9001 with added requirements for the design, development, production, and installation of automotive-related products.
- AS9100: A widely recognized QMS standard for the aerospace industry. It is based on ISO 9001 with added requirements for aircraft, space, and defense products.
Why Is a QMS Important?
A QMS offers many benefits for businesses of all sizes.
First, it helps businesses provide consistent quality in products and services, which builds trust and satisfaction among customers. This consistency helps to strengthen customer loyalty and improve an organization’s reputation in the market.
Plus, a QMS supports compliance efforts, and, when implemented effectively, it can help towards meeting the various requirements of applicable regulations or standards.
A QMS can provide the structure small businesses need to grow sustainably, while larger enterprises can use it to keep operations running smoothly across multiple locations and departments.
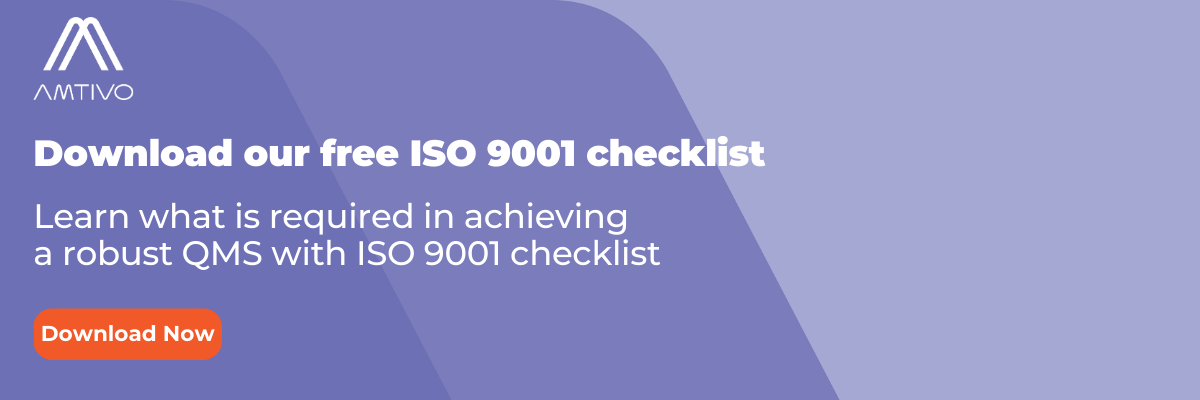
How Does a QMS Work?
A Quality Management System (QMS) works by creating a structured framework that helps an organization improve its processes and performance to meet customer and regulatory requirements.
Here’s how it works:
- Documentation: A QMS sets up written procedures and standards that explain how tasks and processes should be performed for consistent quality.
- Process Management: It involves identifying, managing, and improving key processes that affect quality. This helps processes work efficiently and effectively.
- Performance Measurement: The QMS includes ways to monitor and measure performance against goals and standards. This might involve collecting data, analyzing it, and creating reports.
- Continual Improvement: A QMS encourages ongoing evaluation and improvements in processes and products, using tools like the PDCA (Plan, Do, Check, Act) cycle.
- Risk Management: A QMS helps identify potential quality risks and puts in place strategies to reduce these risks.
- Customer Focus: The system means that customer needs and satisfaction are at the center of all operations and improvements.
- Employee Involvement: A QMS depends on the involvement and commitment of employees at all levels, creating a culture of quality and accountability.
By following the PDCA cycle, businesses can consistently move towards higher quality and efficiency standards, making decisions based on data to support their goals.
The PDCA Cycle
At the heart of an effective QMS is the PDCA (Plan, Do, Check, Act) cycle, a continual improvement process that helps organizations improve their processes over time.
- Plan: Find opportunities for improvement and set the goals and processes needed to deliver results that meet customer needs and company policies.
- Do: Implement the planned processes and begin gathering performance data.
- Check: Monitor and measure processes and products against policies, objectives, and requirements, and report the results.
- Act: Take steps to continually improve performance, using lessons learned in future planning.
Here is an example of PDCA in practice:
A manufacturing business used the PDCA cycle to reduce product defects.
- Plan: The business identified a goal to reduce defects by 20% by introducing a training program for operators.
- Do: They launched the training program and a quality checklist on one production line.
- Check: After a month, a 15% reduction in defects in the pilot line was observed.
- Act: The business expanded the training and checklist to all lines, incorporating ongoing feedback for continual improvement.
How to Implement a QMS
Setting up a Quality Management System (QMS) can be challenging, especially for organizations that are new to quality management or have complex processes.
The typical steps involved are:
- Define Quality Goals: Start by identifying what quality means for your organization and what you want to achieve. This could include improving customer satisfaction, reducing defects, or improving efficiency.
- Get Leadership Support: Make sure top management is committed to quality efforts. Their support is necessary for allocating resources and creating a quality-focused culture.
- Identify and Map Processes: Identify and map out the main processes in your organization. Understand how these processes work together and where you can make improvements.
- Create Documentation: Write documents that outline procedures, policies, and work instructions. This helps to standardize processes for consistency.
- Train Employees: Train employees on the new processes and their roles within the QMS. Regular training helps everyone follow the system properly.
- Implement Processes: Start using the QMS in everyday operations. Encourage employees to follow the documented procedures and share feedback about any challenges.
- Track Performance: Set up ways to measure how well processes are working. Use data to check performance and find areas for improvement.
- Conduct Reviews: Conduct regular internal audits to check compliance and effectiveness. Hold management meetings to discuss findings and make needed adjustments.
- Continual Improvement: Foster a culture of ongoing improvement. Use feedback and performance data to keep refining the QMS.
- Listen to Your Customers: Collect and analyze customer feedback to help you build a QMS that meets their needs. Use this information to drive improvements.
Discover more about implementing an ISO 9001-certified QMS.
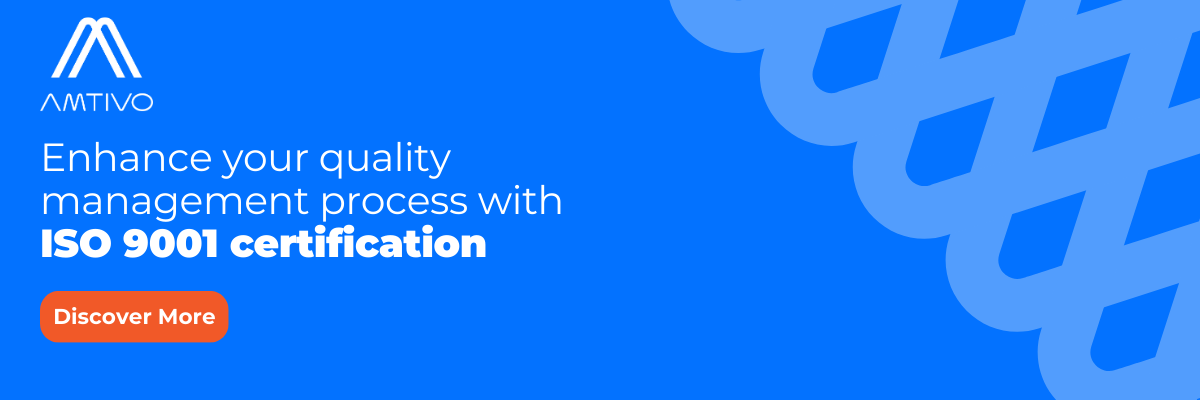
Benefits of a QMS
Implementing a QMS offers several practical advantages, each contributing to the overall success of the organization.
Benefits include:
- Increased Customer Trust: A QMS helps businesses maintain consistent quality of products and services, which builds trust and satisfaction among customers, leading to repeat business and referrals.
- Operational Efficiency: By standardizing processes, a QMS helps reduce waste and improve resource usage, saving money and improving productivity.
- Smarter Decisions: With a QMS, businesses can use data to make informed decisions, allowing for strategic planning and improved outcomes.
- Better Risk Management: A structured QMS spots potential problems early, letting you take action to prevent disruptions.
- New Business Opportunities: A certified QMS, such as ISO 9001, demonstrates a commitment to quality management practices. This may support credibility with prospective clients, partners, or regulators.. Many organizations, including government agencies and international companies, see a QMS as a sign of reliability. In some industries, you might need ISO certification to work with certain clients.
Learn more about the benefits of an ISO 9001-certified QMS.
A Quality Management System is not just a set of procedures but a comprehensive approach to achieving quality in every aspect of your business. By implementing a QMS, you not only improve the quality of your products and services but also strengthen your organization’s resilience and competitiveness in the marketplace.
Whether you are seeking ISO certification or simply aiming to improve your operations, investing in a QMS is a great way to help your company achieve its business goals.
Get started on your journey to ISO 9001 certification—get a quote today or contact our team of experts to discuss your needs.