A Quality Management System (QMS) can be an essential part of everyday operations for businesses that want to boost product quality and efficiency.
It gives you a straightforward way to maintain high quality in everything you do while helping you deliver products and services that comply with industry regulations. Implementing internationally recognized standards like ISO 9001 or IATF 16949 can further enhance these efforts by providing a structured management system for quality management.
If you’re keen to keep your organization evolving and improving, an efficient QMS can be a powerful tool to help drive growth.
So, what do you need to know about QMS implementation? Read on as we explain the steps involved and the key considerations to help you establish a QMS effectively in your business.
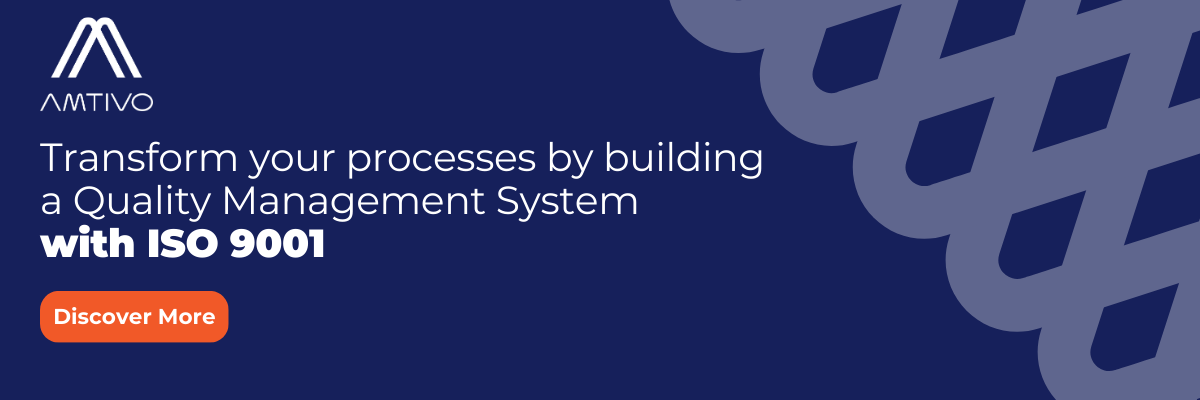
Step-by-Step Guide for QMS Implementation
1. Define and Map Your Processes
Defining and mapping processes is the first fundamental step in QMS implementation, as it lays the groundwork for the development and refinement of your system. This step involves looking at your business as a whole and examining how each operation connects. By doing this, you can identify inefficiencies or hurdles that could be hindering performance.
Visual representation techniques like process maps and flowcharts are important tools to use at this stage. By helping you see how each step in a process connects to the next, they can give you a clear understanding of your business operations and help you improve communication across the business.
2. Define Your Quality Policy
A clearly defined quality policy underpins your business’s commitment to quality and reflects your mission and values. By outlining these commitments, the policy acts as a benchmark that provides clarity around your quality management efforts. It helps everyone in the business understand the standard expected and their role in achieving it.
When it comes to ISO standards for QMS, companies aiming to achieve ISO 9001 certification would need to develop a quality policy that aligns with both customer satisfaction and regulatory compliance.
For example: a quality policy might state, ‘We are committed to delivering products that meet or exceed customer expectations and comply with industry standards.’ However, every business will tailor their policy to reflect its own specific goals and values.
Read our guide on how to write an ISO 9001 quality policy.
3. Define Your Quality Objectives
Quality objectives are the specific, measurable goals that drive your business’s commitment to quality. They should be clear and achievable, aligning with your overall business strategy. These objectives allow you to track and maintain progress.
Your organization might have several quality objectives depending on its size, scope, and strategic goals, focusing on various aspects such as compliance, innovation, and customer satisfaction.
For example: a manufacturing company might include an objective aiming to improve on-time delivery rates by streamlining supply chain operations, while a food producer might include a point about boosting process efficiency through waste reduction strategies over a set period.
Regularly reviewing quality objectives is crucial to keeping them relevant and helps team members stay focused on achieving them.
Want to know more about Quality Management? Read: The 7 Principles of Quality Management.
4. Develop Metrics to Track CSF Data
Critical Success Factors (CSFs) are the essential elements that drive your organization’s success. To effectively manage these factors, it’s important to develop metrics that provide data-driven insights. These metrics will help you measure progress toward your quality objectives and inform strategic decision-making.
An example might be defect reduction rate or on-time delivery—metrics that provide insight into operational performance aligned with quality goals.
5. Identify Potential Defects Within Each Process
Identifying defects in each process is crucial for maintaining quality standards. A defect is any deviation from expected outcomes that affects product quality. By understanding where and why defects occur, you can implement corrective actions to prevent them.
For example, under ISO 13485—the standard for quality management for medical devices—identifying and addressing defects is critical for the safety and reliability of medical products.
Once defects are defined, targeted strategies can be developed to prevent them from recurring. An example of this might include revising company procedures or improving training for staff. This proactive approach helps maintain quality, improve efficiency and strengthen customer trust.
For instance, in a manufacturing company, identifying defects like dimensional inaccuracies could allow for corrective actions, such as recalibrating machines.
6. Create Documents and Records
Thorough documentation is essential for a robust QMS. Developing comprehensive records to capture procedures, policies, and standards helps employee understand their roles and responsibilities. This documentation also supports compliance and is a vital resource for training new staff and conducting effective audits.
Maintaining detailed records helps organizations streamline operations, adapt, and support strategic decisions. Key documents for a QMS can include the Quality Manual, Standard Operating Procedures (SOPs), Work Instructions, Quality Policy, Process Maps, and Internal Audit Reports.
7. Define Quality Processes
Defining quality processes is a crucial step in effective QMS implementation. A business might start by establishing key processes like internal audits, which help regularly check that its operations meet quality standards and identify areas for improvement. Corrective actions are essential for addressing any noncomfomities that arise and resolving them effectively to prevent them from happening again.
Plus, robust communication strategies are vital. They keep everyone informed about quality objectives, process changes, and the outcomes of audits and corrective actions. Together, these processes mean a QMS is well-monitored and continually improved.
Discover more about corrective and preventive actions and how they work in an ISO 9001 QMS.
8. Determine Training Needs
An effective QMS relies on skilled employees. To achieve this, a key step is to identify and address training needs across an organization. Assessing current skill levels and identifying gaps that might affect quality performance helps everyone understand their specific role in maintaining and improving quality standards.
For example, employees may need training on specific quality standards like ISO 9001, or internal auditing techniques and practical data analysis so they can effectively support the QMS.
Ongoing training keeps teams up-to-date with the latest practices and promotes accountability as employees can feel empowered to drive process improvements.
9. Use the QMS Effectively
To truly benefit from a QMS, it must be integrated into daily business operations, so quality considerations are a fundamental part of every decision. This means consistently applying QMS principles across all levels, with guidance from senior leadership, from the factory floor to the boardroom. This involves having regular reviews to align operations with goals and market changes.
Using a QMS effectively also means building a culture of continual improvement throughout your business. This involves creating feedback loops where data-driven insights lead to real changes in your operations. Encouraging employees at all levels to participate in quality initiatives helps keep a QMS strong and adaptable.
Learn about the role of customer feedback in quality management.
10. Measure, Monitor, and Improve Performance
Measuring and monitoring performance is crucial to your QMS implementation plans. Data can help you track how well your processes are working and spot areas for improvement.
Ongoing data analysis can also help verify that your organization is meeting quality standards and adapting to any changes in your business environment.
Regularly reviewing performance data helps you decide where to focus your efforts and which part of your business to target. For example, you might consider implementing initiatives to reduce waste, improve efficiency, or boost customer satisfaction. Over time, these adjustments can lead to higher quality standards and better overall performance, so your business remains competitive.
Learn more about quality management and related terms with our guide to Quality Management vs. Quality Control vs. Quality Assurance—What’s the Difference?
Tools for QMS
The following tools are typically used in QMS implementation to help organizations meet the requirements of various ISO standards through effective management, control, and continual improvement of quality processes.
Process Maps and Flowcharts
What are they? Visual tools to depict the sequence of steps in a process, helping to identify bottlenecks and streamline operations.
How do they work? These tools provide clarity on how different operations interact, making it easier to optimize processes. In ISO 9001, process maps support the approach by promoting efficiency and alignment with quality objectives.
Failure Modes and Effects Analysis (FMEA)
What is it? A systematic method for identifying potential failures in a process and assessing their impact.
How does it work? FMEA helps businesses prioritize risks based on their severity, occurrence, and detection so they can be mitigated. In ISO 13485 for medical devices, FMEA is often used as part of risk management to support product safety and reliability.
Control Charts
What are they? Statistical tools used to monitor and control process performance over time.
How do they work? By plotting data, control charts help identify variations and trends, signaling when a process is out of control.
Checklists
What are they? Simple lists that help to check that all necessary steps are completed.
How do they work? Checklists help maintain consistency and reduce errors, especially in complex or repetitive tasks. They are used in various ISO standards for QMS to promote consistency and compliance with processes.
Root Cause Analysis (RCA)
What is it? A method for identifying the underlying causes of a problem or defect.
How does it work? By analyzing the root cause, organizations can implement corrective actions to prevent problems from occurring again.
Statistical Process Control (SPC)
What is it? A method involving statistical techniques to monitor and control a process.
How does it work? SPC analyzes data from production processes to spot variations that could affect quality. In IATF 16949 for the automotive industry, SPC is used to deliver high-quality standards in manufacturing processes.
Avoid issues when implementing your QMS. Read our guide to the 7 common ISO 9001 implementation mistakes.
Ready to Start Your QMS Implementation?
Successful QMS implementation relies on strong leadership and ongoing commitment. By engaging employees at all levels and fostering a culture of quality, you can help maintain an effective QMS for your business—one that continues to improve, ultimately leading to increased customer satisfaction and a competitive advantage.
Get started on your journey to certification—get a quote today or contact our team of experts to discuss your needs.