Robust quality management is important for any business aiming for long-term success and profitability. Effective implementation of a Quality Management System (QMS) is a dependable strategy to help organizations achieve this goal.
Seven principles of quality management are central to implementing a robust QMS. These principles form the backbone of the ISO 9000 family of standards, particularly ISO 9001—the most widely adopted QMS standard.
These principles aim to improve organizational performance, consistency and overall management effectiveness, so they are also broadly applicable to various management standards beyond quality, including ISO 14001 (environmental management) and ISO 45001 (occupational health and safety), although those standards have their own specific principles.
In this guide, we’ll discuss these seven quality management principles in detail and explain their roles in a QMS.
Whether you’re just starting with quality management or looking to improve what you already do, knowing these principles is essential to getting the most out of your quality management initiatives.
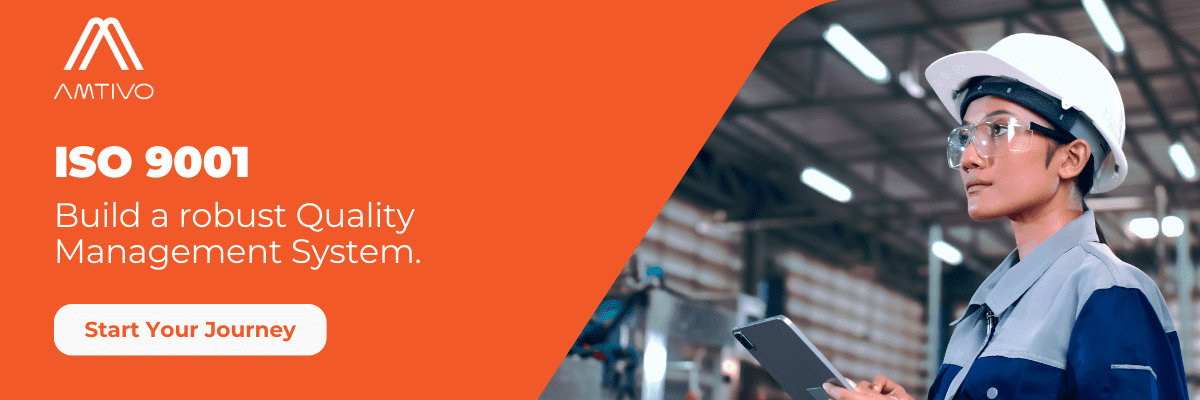
Core Quality Management Principles
Understanding the seven core quality management principles can help you implement a strong Quality Management System that benefits your business.
1. Customer Focus
A strong emphasis on customer focus is central to any Quality Management System. This principle highlights the need to understand and meet customer needs and expectations.
Businesses that prioritize customer focus aim to go beyond customer requirements, improving customer satisfaction while building loyalty and trust. As a result, companies can stand out in the market by consistently delivering value.
One of the best ways to understand your customers is to listen carefully to them, using feedback tools like surveys, direct interactions, and reviews. By engaging with customers this way, you can gather valuable insights into customer preferences and pain points, allowing you to tailor your products and services accordingly.
Adopting a customer-centric approach can help organizations anticipate future customer needs, keep customers satisfied and help the business succeed in the long term.
Example: A software development company implements a customer feedback loop in its development process. By actively engaging with users during beta testing and incorporating their feedback, the company may improve its product, boosting customer satisfaction scores. This approach aligns well with ISO 9001:2015 requirements for customer communication and satisfaction monitoring.
2. Leadership
Leadership plays a crucial role in setting the direction and building a culture of quality in an organization. This key principle of a QMS highlights the need for leaders to create a clear vision, making sure the organization’s objectives match its quality goals. Good leaders inspire and empower employees, provide resources, and remove barriers to improvement.
Leaders can encourage innovation and continual improvement by promoting a culture of openness and collaboration, helping the business deliver high-quality products or services.
Example: A manufacturing plant manager implements daily leadership walks through the facility, engaging directly with employees about quality concerns. This visibility and accessibility could result in a significant reduction in quality-related incidents and improved employee engagement scores.
3. Engagement of People
A fundamental QMS principle recognizes the value of involving all employees in achieving quality objectives. Engaged employees can be more committed, motivated, and aligned with the organization’s goals.
To help encourage involvement, organizations can promote:
- Open communication
- Offer opportunities for professional growth
- Recognize and reward contributions to quality initiatives.
Including employees in quality management decision-making and problem-solving can help boost job satisfaction and support continual improvement.
Example: A healthcare facility introduced cross-functional quality circles that allow staff from different departments to collaborate on quality improvement projects. This initiative can improve patient care metrics and boost staff retention rates.
4. Process Approach
This principle stresses the need to understand and manage interconnected processes as part of a unified system. By clearly defining, documenting, and improving processes, businesses can align activities to meet their quality goals.
The process approach helps organizations to:
- Spot inefficiencies
- Eliminate unnecessary steps
- Streamline operations
Improving processes effectively can help companies make better products, reduce waste, and increase customer satisfaction.
This approach also encourages a culture of accountability and transparency, as employees clearly understand their roles and responsibilities within the larger system.
Example: An automotive parts supplier maps their production process, identifying key interaction points and potential bottlenecks. This systematic approach can help reduce defects and improve delivery times.
5. Improvement
Continual improvement is a key part of quality management, encouraging businesses to boost their performance and keep up with changing market conditions. This principle promotes actively looking for ways to improve and implement effective solutions. By adopting a culture of innovation and learning, businesses can achieve lasting growth and stay competitive.
Many organizations establish processes to:
- Track performance
- Set improvement goals
- Measure progress
These are methods to support continual improvement. Creating an environment where employees feel free to experiment, learn from mistakes, and share best practices can help any business speed up its improvement efforts and deliver lasting value to customers.
Example: A food processing company implements a suggestion system where employees can propose improvement ideas. Employee suggestions can help to boost product quality, reduce waste, and improve food safety compliance.
6. Evidence-Based Decision Making
This principle highlights the importance of using accurate and reliable data to guide decisions. By relying on evidence rather than assumptions or guesses, businesses can minimize risks and make better choices.
Organizations could consider setting up systems for collecting and analyzing data. The specifics of these can vary depending on the size of the business, its complexity, and the industry. Using data analytics, companies can:
- Understand trends
- Assess performance
- Find areas for improvement
This data-driven approach helps businesses make informed decisions that match their quality goals and overall strategy.
Example: A retail chain uses data analytics to track product quality complaints across all stores. This evidence-based approach helps them identify systematic issues, which can help to reduce customer complaints. This practice supports requirements across multiple ISO standards for measurement and analysis.
7. Relationship Management
Managing stakeholder relationships is essential for achieving quality objectives and driving long-term success.
This principle is about creating strong partnerships with:
- Customers
- Suppliers
- Employees
- Other important stakeholders
By engaging with stakeholders, businesses can align their quality goals with their needs, encouraging cooperation and teamwork. Strong supplier relationships can help to improve supply chain efficiency, while positive internal relationships can boost employee morale and loyalty.
Effective relationship management ultimately supports innovation, adaptability, and achieving strategic goals.
Example: A construction company develops a supplier rating system based on quality metrics, delivery performance, and sustainability practices. This system could improve its supply chain reliability.
![]() |
Quality Management Principles—Next Steps
The seven quality management principles provide a clear guide and strong foundation for helping an organization run smoothly and effectively.
These principles are the guiding philosophies behind ISO 9001 and other related standards—they help businesses set up and run a Quality Management System effectively. By following these principles, your organization could improve and maintain consistency, which can be valuable when working towards certification.
To learn more about how an ISO 9001-certified QMS could help your business, read our guide to what makes a Quality Management System and explore our list of ISO 9001 training courses to start applying these principles today.
Here are some of our other resources you might also find helpful
- Quality and Total Quality Management—QMS vs TQM
- ISO 9001 Beginner’s Guide
- What Is the Plan, Do, Check, Act Cycle?
- ISO 9001 Checklist
- Benefits of ISO 9001 Certification